Block machines handle variations in block thickness through precise control mechanisms and adjustments in the production process.
Here are key ways in which block machines manage variations in block thickness:
- Adjustable Molds:
- Many block machines come with adjustable molds that allow operators to modify the dimensions of the produced blocks. This feature enables flexibility in accommodating variations in thickness.
- Calibration and Settings:
- Block machines are equipped with calibration settings that control the height and pressure applied during the compaction and molding process. Operators can fine-tune these settings to achieve the desired block thickness.
- Automated Controls:
- Modern block machines often feature automated controls, including Programmable Logic Controllers (PLCs). These controls enable precise adjustments, ensuring consistency in block thickness throughout the production run.
- Vibration Control:
- Vibration is a crucial element in the compaction process. Block machines regulate the intensity and duration of vibrations, influencing the density and thickness of the blocks. Fine-tuning vibration parameters helps maintain uniform thickness.
- Hydraulic Pressure Control:
- Hydraulic systems in block machines control the pressure applied to the raw materials within the mold. By regulating hydraulic pressure, operators can manage the density and thickness of the blocks being produced.
- Quality Control Sensors:
- Some block machines are equipped with sensors that monitor block dimensions in real-time. block machinery These sensors provide feedback to the control system, allowing immediate adjustments to compensate for variations in thickness.
- Material Feed Control:
- The rate at which raw materials are fed into the block machine influences the thickness of the blocks. Control mechanisms are in place to manage material feed speed, ensuring consistent block dimensions.
- Operator Monitoring and Adjustment:
- Skilled operators play a crucial role in monitoring the production process. They can visually inspect blocks, measure thickness, and make real-time adjustments to the machine settings as needed.
- Customization Features:
- Some block machines come with customization features that allow users to produce blocks with specific dimensions. This customization capability is valuable when dealing with variations in thickness requirements.
- Regular Maintenance:
- Regular maintenance of the block machine, including checking and calibrating components, helps prevent wear and tear that could affect the machine’s ability to maintain consistent block thickness.
- Material Composition Control:
- Ensuring the uniformity of raw materials, including the mix of aggregates and cement, contributes to maintaining consistent block thickness. Quality control measures in material preparation are critical.
- Testing and Sampling Protocols:
- Implementing testing and sampling protocols during production runs helps identify variations early on. This proactive approach allows operators to make adjustments before a significant quantity of blocks is produced.
By incorporating these control measures and features, block machines can effectively handle variations in block thickness, ensuring that the produced blocks meet the specified quality and dimensional requirements. Advanced technologies and automation further enhance the precision and efficiency of this process.
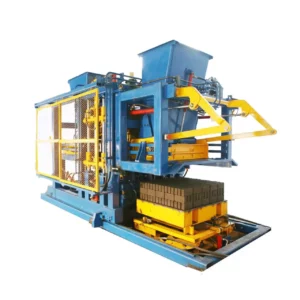