Curing is a crucial process in the production of concrete blocks to ensure their strength and durability. Proper curing allows the blocks to attain their desired strength and durability characteristics. Here’s how blocks are cured:
- Initial Setting:
- After the concrete blocks are formed in the molds and compacted, they go through an initial setting phase. During this phase, the concrete begins to harden, but it is not yet fully cured.
- Demolding:
- Once the blocks have undergone initial setting, they are demolded. This involves removing the blocks from the molds while being careful not to damage their surfaces.
- Water Curing:
- The most common method for curing concrete blocks is water curing. The blocks are placed in a controlled environment where they are continuously moistened with water. This can be achieved through various methods:
- Water Ponding: Blocks are placed in shallow ponds of water.
- Sprinklers or Drip Systems: Water is continuously sprayed or dripped onto the blocks.
- Covered Wet Burlap or Fabric: Blocks are covered with wet burlap or fabric to retain moisture.
- The most common method for curing concrete blocks is water curing. The blocks are placed in a controlled environment where they are continuously moistened with water. This can be achieved through various methods:
- Duration of Curing:
- The duration of water curing is crucial. Typically, concrete blocks are cured for a specified period, such as 7, 14, or 28 days. The duration depends on factors like the type of concrete mix and desired strength.
- Temperature Control:
- Curing is often done at controlled temperatures. While warmer temperatures generally accelerate the curing process, block making machine it’s essential to avoid rapid drying or excessive heat, as it can lead to cracking.
- Humidity Control:
- Maintaining high humidity levels during curing is essential. This prevents the blocks from drying out too quickly and allows the cementitious materials to undergo proper hydration.
- Steam Curing:
- In some cases, especially for precast concrete products, steam curing may be employed. This involves exposing the blocks to high-temperature steam, accelerating the curing process.
- Curing Compounds:
- Some curing compounds can be applied to the surfaces of the blocks to retain moisture and promote proper curing. These compounds form a protective film that helps prevent water evaporation.
- Covering and Insulation:
- Blocks can be covered with insulating materials to reduce heat loss during curing. This is particularly important in cold climates to maintain a conducive curing environment.
- Quality Control Checks:
- Quality control checks are conducted during and after the curing process. This may include compressive strength tests to ensure that the blocks meet specified strength requirements.
- Final Inspection:
- After the curing period, the blocks undergo a final inspection to ensure that they have attained the required strength and durability. This involves visual inspection and testing.
Proper curing is essential to achieving the designed strength and durability of concrete blocks. The controlled application of moisture, temperature, and time during the curing process allows the cementitious materials to hydrate fully, resulting in a strong and durable end product.
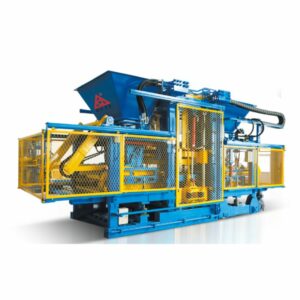